Use Cases#
Amazon operates and orchestrates a global network of warehouses that include over 200 fulfillment centers handling tens of millions of packages per day. This complex operation requires over half a million mobile drive robots to support warehouse logistics. By building AI-enabled digital twins of their warehouses using NVIDIA Omniverse Enterprise, they can optimize warehouse design and flow, train more intelligent robot assistance and gain overall productivity.
Another company with a complex network of hundreds of distribution centers is PepsiCo. Since one billion PepsiCo products are consumed daily, improving throughput, reducing downtime, and reducing the energy consumption of their distribution centers are critical. With NVIDIA partner Kinetic Vision, PepsiCo is developing an AI-powered digital twin of their distribution centers in NVIDIA Omniverse Enterprise and optimizing operations with NVIDIA Metropolis and TAO.
While demos of warehouse digital twins at the scale of Amazon Robotics and PepsiCo can serve as a great inspiration, highlighting the art of the possible, digital twins brings significant business value to warehouses at every scale. We worked with our partners and customers and learned a great deal about various types of warehouse implementations. The complexity of these warehouses ranges from small, primarily manual operations to large facilities enhanced with sensors and automation. Through partner feedback and analysis of many warehouses operating patterns, we have compiled a preliminary set of scenarios that our warehouse digital twins can be used.
Each warehouse may have its own set of opportunities for improvement and optimization. Still, we can simplify and generalize some standard warehouse functions and the basic requirements needed to support those functions. A warehouse is used to store products or inventory which need to be slotted, stocked, and moved within the environment. Then depending on the type of inventories, the products may need to be packaged before shipment. Basic infrastructure is required to support those warehouse functions, including a building, machinery, and tools. Operating the warehouse may be manual, simply relying on warehouse workers; it may be completely autonomous or hybrid, with humans and machinery working in concert. Some operations may be triggered by triggers from supply chain connected software and/or systems.
In addition to those opportunities, the overall functions of a warehouse may be threatened by some challenges and risks, such as labor shortages, supply chain disruptions, operation disruption, natural disasters, and space limitations.
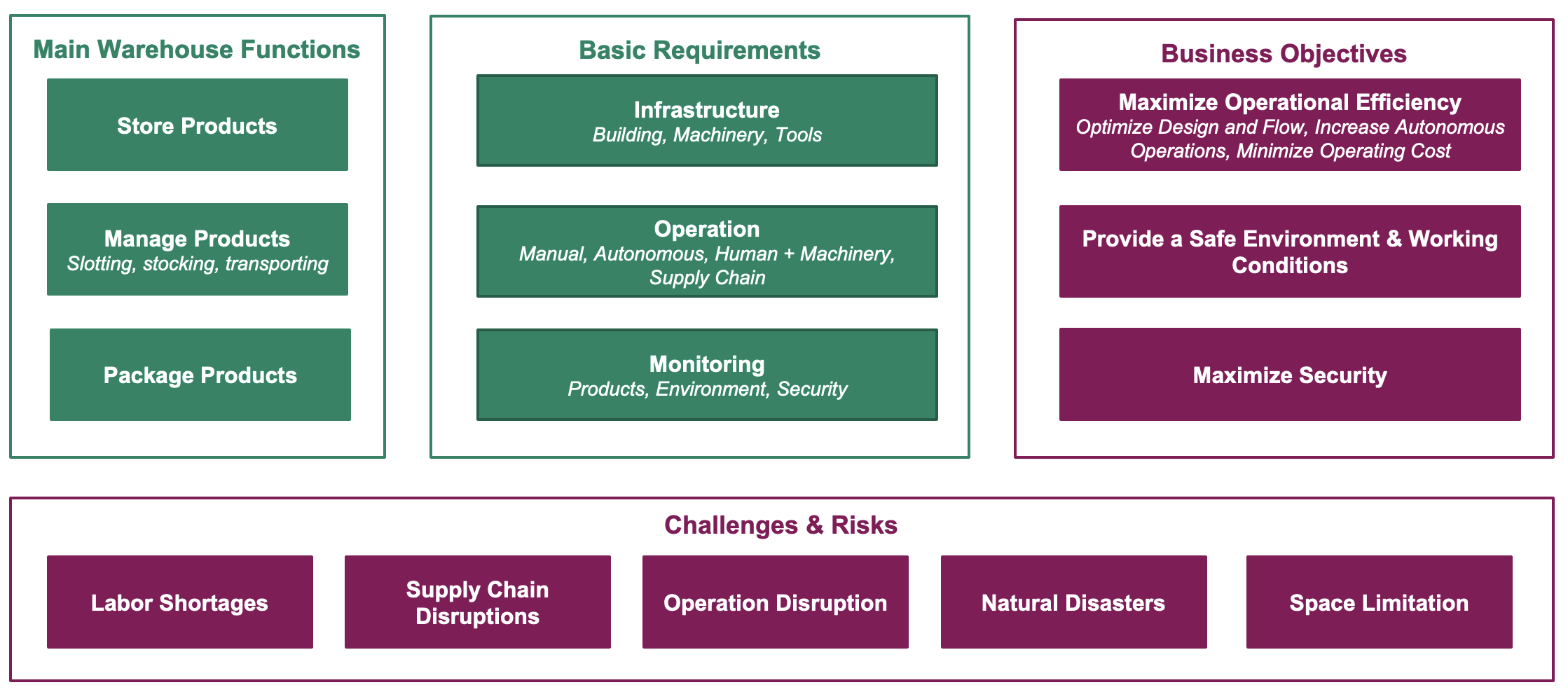
Now that we simplified the warehouse functions, requirements, challenges and risks, here are some sample use cases that could be best solved using a digital twin to maximize operational efficiency, provide a safe environment and working conditions, and maximize security, all of which are key business objectives of warehouse operators.
Optimizing design and flow enables warehouse owners or operators to maximize inventory storage capability, increase throughput, and minimize space, equipment, and labor needed to carry out business operations. Here are some examples of use cases to address those needs:
Spatial design and optimization support the warehouse’s entire operation and end-to-end product circulation.
Designing and optimizing traffic flow for workers, machinery, and robots for safe circulation in a warehouse environment.
Designing and optimizing the end-to-end flow process of products and the required machinery, robots, and humans to carry out the operation.
Optimizing space utilization and maximizing the storage capacity of a warehouse.
Monitoring, analyzing, predicting, and adjusting traffic flow design based on fluctuating warehouse productivity levels.
Designing a warehouse layout that is adaptive and customizable based on demand fluctuation.
Designing and validating optimal lighting to support various warehouse operations.
Designing and validating proper ventilation flow.
Predicting possible congestion scenarios and then creating and validating mitigation plans.
Increasing Automation is another way of maximizing operational efficiency. It may be used to enable various functions within a warehouse which include but are not limited to:
Inspecting and detecting product defects.
Identifying products to be picked or assembled for an order.
Inspecting assembled orders for accuracy (quantity and type).
Applying an adequate gripping strength based on each product’s physics.
Customizing packaging methodology/material/protection based on products’ physical properties.
Automating the packaging process
Picking and placing products.
Transporting inventory in optimized routes.
To minimize the operating cost of a warehouse, example use cases include:
Increase energy efficiency by optimizing operation.
Optimize operation and number of workers.
Reduce inventory damages.
Providing a safe environment and working conditions is another key business objective and requirement set by government agencies such as OSHA. By examining the top causes of worker injuries within a warehouse, here are some examples of use cases to increase safety:
Reducing Human Errors:
Monitor proper operation of heavy equipment
Monitor wearing adequate safety equipment compliance in designated areas.
Slips and Trips:
Evaluate visibility of caution tapes & hazard signs
Optimize lighting intensity and coverage.
Falling Objects:
Conduct earthquake proofing of facility.
Design and evaluate navigation routes around highly dynamic and fast-moving locations.
Fire:
Design and ensure warehouse flue space compliance.
Optimize placement of portable fire extinguishers.
Plan and evaluate evacuation routes.
Harmful Substances:
Design chemical storage areas and evaluate monitoring and containment capabilities in case of spillage.
Design “First Aid Stations” and simulate various scenarios to optimize the design.
Design and evaluate evacuation routes based on different scenarios.
Safety Education & Training:
Train employees on how to move and store heavy materials – and the equipment used to move them safely.
Train employees on how to operate machinery.
Train employees on warehouse accident protocols.
Another type of safety measure to address is workers’ ergonomics. Digital twins can help by enabling workspace customization to support individual works, motion planning, and analysis of job tasks. Interactive training on proper techniques for lifting, pushing, pulling, holding, carrying, or throwing objects with real-time feedback on posture for safe ergonomics.
Maximizing security is another critical business objective. Depending on the type of warehouse and the inventory stored, the level of security requirements may vary. Here are a couple of use cases to maximize security.
Design and validate the placement of cameras and other monitoring equipment to provide proper space coverage.
Design and evaluate plans in case of security breaches.