Materials Best Practices#
Creating Materials for Simulation#
Materials destined for simulation have different requirements from materials used solely for design visualization or film/video game usage. Beyond just the visual surface appearance, SimReady materials also need to accommodate non-visual sensor attributes as well as physical material properties needed for physics simulations.
Non-visual sensor attributes are required so that vehicle and robotics sensors that use frequencies outside the visible spectrum and provide reflections from LiDAR, RADAR and other transducers can get proper data returns from 3D assets in their scenes to help guide them.
Physical materials are also needed to help inform runtime simulations how 3D assets should interact physically by defining friction and restitution attributes of those material substrates like wood or metal. As you start to create your SimReady materials, keep these simple rules in mind.
Quick Tips and Techniques#
The guidelines for materials in a simulation application are much the same as for a real-time game engine or even an offline renderer. Performance is always a consideration, as well as memory consumption at runtime.
Key things to keep in mind:
Keep shader graphs simple
Keep the bitmaps efficient (don’t create 8K maps when 2K or 4K will do)
Use an RGB value, or reuse a bitmap when you can
We’ll touch on each of these and why they can be critical to the performance of a simulation. Additionally, as you’ll see in the next section, Material Segmentation is a core requirement for geometry and materials in a SimReady 3D asset.
In the context of using Omniverse as a simulation platform, it works best on high-performance systems with multiple GPUs. However, developer machines may be more resource-limited, and creators should consider the simulation’s target hardware.
As systems that run simulations get more powerful, limitations tend to disappear, objects become more detailed, shaders more complex, and textures ever larger without an impact on performance. That said, objects, materials, and textures should always be good citizens of the entire ecosystem and not cause performance or resource issues with little benefit.
Always consider shader complexity and texture map size at every step and the requirements for the asset’s use case.
Introducing Material Segmentation#
To help future-proof and ensure a smooth upgrade to simulator products, creators should consider a requirement called “Material Segmentation” throughout asset development.
Simulators require that creators separate geometry by substrate type. In other words, if you have an asset that has both wood and plastic materials, you should have two geometry prims to represent it so you can apply each material to the appropriate part. Each object can have only one material, so what may have used Multi/Sub-Object materials and monolithic ORM surfaces may require revisions.
Using an ORM map to define transparent, shiny, and metallic areas will still render correctly in the simulator. However, the simulator needs to know the real-world substrate type of the underlying geometry (metal, glass, plastic, etc.) and not just how it looks in visible light. They must be separate def mesh
prim objects within the USD with one material for each prim.
The image below is a simulation-ready traffic asset with detailed Albedo, ORM, and Normal bitmaps. The creator separated the materials by the underlying physical type: metal for the body, a retro-reflective plastic reflector, and rubber for the tires:
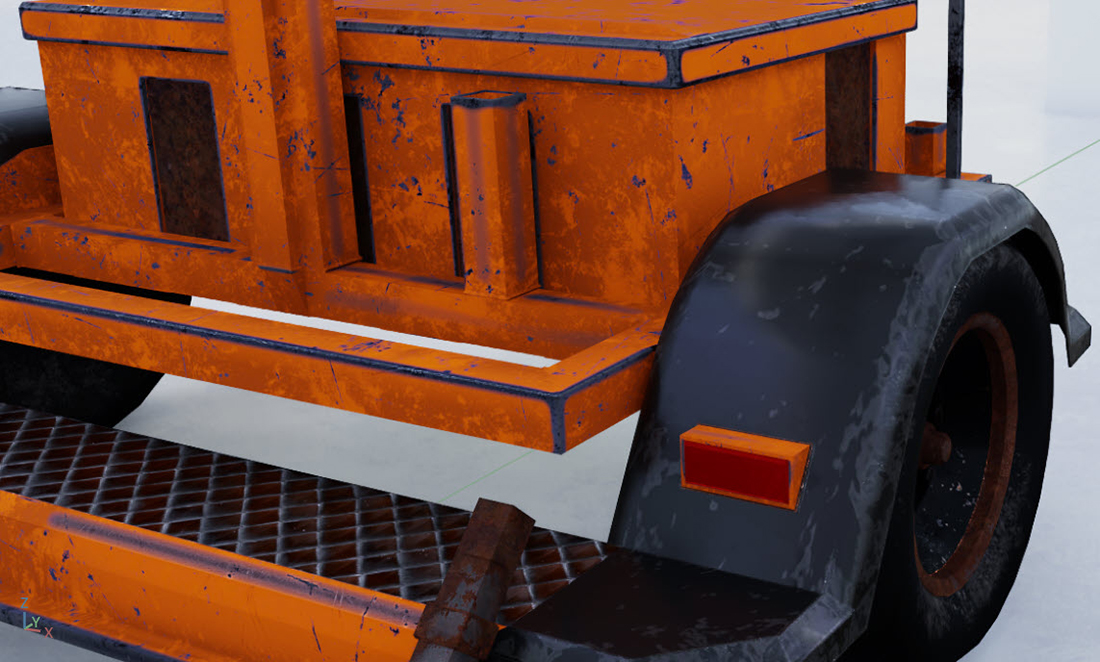
A Simulation-Ready Traffic Asset with Three Materials#
With the objects and materials properly segmented, the simulator can react to the substrates based on the transducers in the simulation.
Below is how the Omniverse Stage looks for this asset, with each mesh object getting one material:
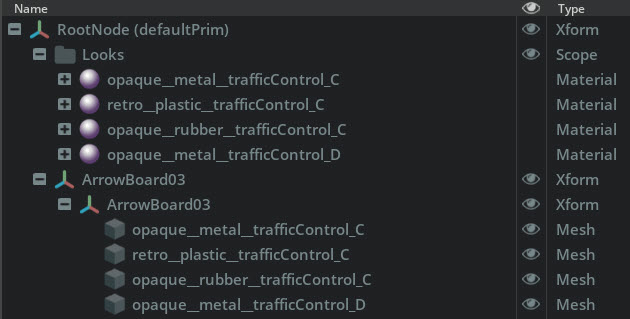
Stage UI For Traffic Asset#
It is worth noting that in the example above, the creator followed a material naming convention that mimicked the geometry names, but this is not required for SimReady assets.
Understanding material segmentation requirements and creating your assets with this in mind from the start will help ensure an easy path to more complex simulations.
Material Naming Conventions#
While SimReady does not enforce a specific material naming schema, we encourage the following methodology to help keep your assets clean and understandable. Following a few rules will help you manage your materials so that they work as expected.
We recommend using material names that are all lowercase and have three sections with underscore symbols between sections. The three sections are defined as follows:
Prefix Material Type, such as
opaque_
Surface Type, such as
metal_
Description, such as
brushed_aluminum
with single underscores instead of spaces.
The material name is opaque_metal_brushed_aluminum
in the example above.
Again, there is no single “right way” to name your materials, but we’ve found that by providing insights into the material type, surface and characteristics it can speed up other workflows and make it easy for consumers of those assets to be able to quickly introspect them for certain attributes.
Understanding Physically-Based Rendering#
Physically-Based Rendering - or PBR - is the process of reproducing real-world direct and indirect lighting, reflections, and surface appearance in a physically real rendered environment. The renderer, materials, and lighting all combine to create photorealistic results.
PBR Rendering in simulators (SimPBR) expand the definition of PBR to include the electromagnetic (EM) spectrum outside visible light to support RADAR, LiDAR, and other transducers.
Getting to know PBR Materials#
A PBR material correctly handles how energy is absorbed, colored, emitted, and reflected by the surface. They produce an energy-accurate result, returning energy into the environment, and when combined with a PBR renderer, they create a natural image with correct lighting and surface interactions.
Because materials like UsdPreviewSurface are “PBR-based” they won’t produce more energy than they take from the environment (unless it is emissive). They will balance the physical energy results as you adjust the materials. Energy conservation is automatic and not something the creator needs to consider.
With a PBR shader, the diffuse albedo color decreases proportionately as reflection increases. If a shader is transmissive, the energy returned in albedo and reflection is adjusted to maintain physically-accurate results.
Creating PBR Materials for Simulation#
If you are creating materials for simulation within the Omniverse platform, you can take advantage of non-visual sensor information, which extend the capabilities to cover vehicle and robotics sensors in a physically-accurate way. They work beyond the visible electromagnetic (EM) spectrum and are managed by the RTX Sensor package. Non-visual sensor information is applied at the Material prim level to inform the RTX Sensors what type of material it represents. Given that the return data isn’t visual, but a data package, trying to ensure accuracy of these attributes can be a challenge for creators.
Use OmniPBR & OmniGlass Shaders#
Materials used in a simulation application should use OmniPBR and OmniGlass for best compatibility. The simpler the shading graph, the better, as this helps ensure fast shading and easy upgrading to upcoming simulation-ready shaders.
For a detailed look at creating and using the OmniPBR material, refer to the Omniverse Material Documentation.
Material Complexity and Performance#
When simulation performance is a priority, the additional time required to render complex materials adds up quickly. When particular objects or materials appear, you may see a drop in viewport frames-per-second (FPS), indicating where an issue may be.
As mentioned, some features can be turned off in the render settings for simulation and then enabled for rendering. Changing selected material settings will benefit simulation, visualization, and viewport performance without changing global options. Refraction and Reflection are two things, in particular, to look for, as well as any options for transparency and sub-surface scattering.
Eliminate IOR#
For OmniGlass materials, an Index of Refraction not at 1.0 or the “Thin Walled” option unchecked, as below, will render much slower than without refraction:
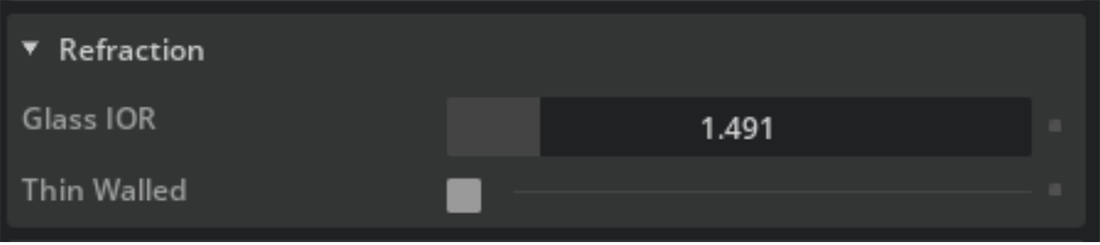
Refraction Settings in OmniGlass#
Translucent plastic and flat sheets of glass, or “window glazing,” should enable the “Thin Walled” checkbox to eliminate refraction, and this is how real-world glazing works.
For OmniPBR, it does not calculate an IOR with transparent areas. However, materials that are not fully opaque or transparent will take more time.
Reduce Reflections#
Use reflections where beneficial, and eliminate them where you can. A glossy paint finish that casts reflection rays will always take more resources than a flat paint finish.
The number of reflections and samples can be changed in the render settings to speed simulations and preserve the look of advanced rendering.
Keep it Simple#
If there is a need for complex shaders for design visualization, special effects, or digital twins, just be aware that you may need to rework the materials to ensure they convert into SimPBR.
An automotive finish will use a material with a Clearcoat option that has reflections, refractions, and interaction with the underlying surface, which also has its shading and reflections.
Sub-Surface Scattering (SSS) is another computation-intensive technique that may need to be limited or eliminated when running a simulation. SSS can be controlled in the render settings to increase performance globally.
Using MDL Files#
If you want portability and control over the look of a surface throughout your project, place the material settings within an MDL file. The advantages are:
Text-based files work well with source control and versioning
Allows for consistency across assets
Can provides baseline template for artists
Separates asset and material workflows
When you use an MDL file in your stage, it brings any defined settings, including texture paths, and changes made to the MDL affect all surfaces that use the MDL.
Working with the USD “over” Workflow#
USD uses a hierarchy where changes made “over” another setting take precedence over lower settings when determining stage composition. Where the settings are within that hierarchy can determine whether they have any effect downstream.
For materials based on an MDL, if you edit any material settings in the USD file, this change will be “over” the settings in the MDL. The corresponding settings in the MDL will no longer affect the USD. This can be confusing if an artist makes a change in an MDL and their assets don’t reflect the change.
In this MDL-driven material below, both the Albedo Map and the Color Tint are modified in the USD, as indicated by the blue square on the right of the Property Panel UI:
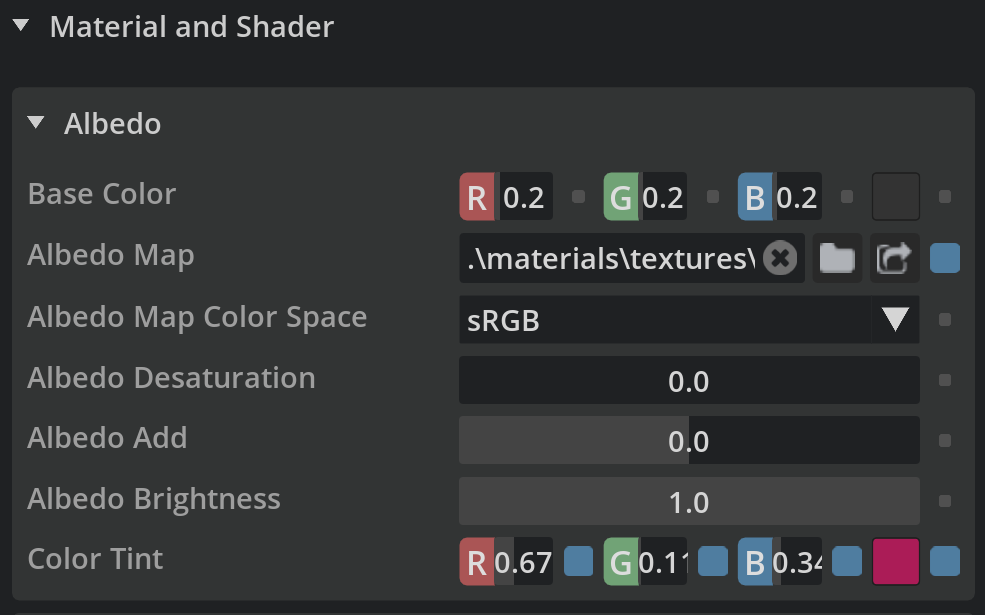
Material Albedo settings with Overrides#
Any changes in the MDL to these two settings will not appear in this USD; since these changes are handled “over” the MDL. This is a feature, not a bug, and essential for artists to understand. Ideally, create a new MDL that reflects the new settings rather than edit and override MDL settings in the USD.
Clicking on the blue square will restore the default settings from the MDL. The USD file may also store default settings independent of the MDL file, so if MDL settings don’t restore correctly, you’ll need to edit the USDA code. Enable the USDA Editor extension in Create and remove any extra default settings:

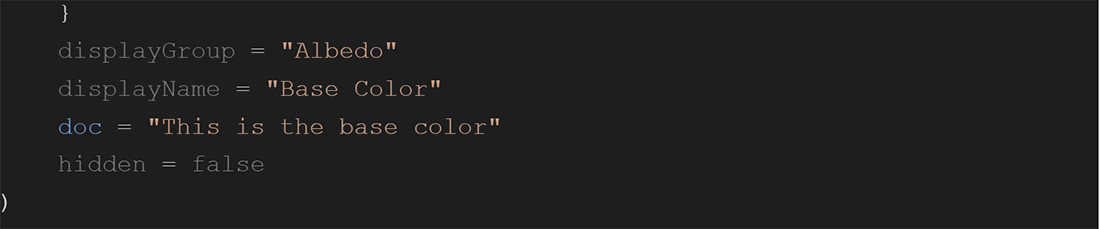
This listing of the shader’s settings from the USDA file has values in the first line overriding the MDL setting (the ‘= (0.90, 0.11, 0.11)’) and a default setting defined below which may be different than in the original MDL (the ‘customData = {}’ section). Although not a common issue, be aware of where settings may be stored and overriding the MDL and its defaults.
Using Textures#
Generally, use tiled texture maps and reuse textures wherever possible. As we’ll see later, even relatively low-resolution bitmaps can be tens of megabytes, resulting in hundreds of megabytes of cached textures for use with the GPU.
Textures created in Substance Designer and Substance Painter make for striking visuals. However, large (4k or larger) monolithic bitmaps can impact resource consumption. Texture painting applications make it easy to add subtle, high-frequency noise patterns in maps, resulting in large files that don’t compress well. Keep the result in mind and where this texture will be used and seen.
Use Direct X for Normals in the Substance project settings, the PBR Roughness, and Metallic workflow, and bake and create all textures at 4k resolution. You can always resize them smaller if desired.
Texture Folders and Paths#
The standard is to place asset-specific MDL files into a materials
subfolder of the USD and bitmaps in a textures
subfolder of materials. All textures in MDL files use relative paths such as ./textures/
or use ./materials/textures/
in the USD. These folder names are in lowercase.
Paths to textures and materials referenced in a USD should be relative to the USD and not a hard-coded path to a server or drive.
Evaluate and change paths in your file when editing the individual asset, not when the asset file is part of another stage and USD has resolved the paths. The paths may be relative when looking at the asset’s USD file, and show a longer full path when the USD is part of a larger stage.
Texture File Types#
Files destined for simulation should be 24 or 32-bit PNG formatted files. Other formats may be supported. However, PNG is reliable, provides lossless compression, and includes additional channels like Opacity when needed. The NVIDIA DRIVE Sim application uses the Alpha channel in the Albedo map for opacity, for instance.
Albedo maps are Gamma corrected sRGB format, and ORM, Normal, and other textures are typically non-Gamma corrected linear - or “raw” - format. The “auto” option in texture settings should be avoided as it is not always able to detect the proper format from some files.
Understanding Texture Sizes#
Currently, you should keep your bitmap textures under 8k by 8k in pixel resolution. However, we recommend images of 4k or less for SimReady assets. Many objects, particularly small or distant objects, may not take advantage of the detail in a 4k bitmap, and we suggest 1k or 2k textures as a baseline dimension.
The use of small, tileable textures is ideal.
Beyond the pixel resolution of the bitmap is the size in megabytes and memory it will use when in your stage. Most objects in a large design visualization or simulation will likely be seen full-screen and studied at length.
Using Texel Density#
For simulation assets, our preferred target Texel Density is 2048 pixels/meter measured at 4k by 4k. The maximum texture resolution is 4k by 4k, and non-square textures are allowed.
Using UDIM#
To achieve the target texel density and keep the resolution to 4k or less on large objects, USD can use UDIMs. In the material’s texture name, simply replace the UDIM number with .<UDIM>
- for example, T_Forklift_A1_Albedo.<UDIM>.png
Reusing Textures#
One of our recommendations is to reuse textures whenever possible and use RGB values where a bitmap is simply a color swatch.
Bitmap reuse and tinting can provide color and surface variation objects without the need for additional bitmaps. For instance, if you have a series of colored plastics, ideally, you wouldn’t have individual ORM and Normal maps if those textures are all the same. The plastic Albedo color bitmap could also use a desaturated texture or be based on a white bitmap and then Color Tinted, rather than using unique images. Controlling the Color Tint value is often how we provide color variants in our props.
Numerous similar or identical maps not only use space in your Omniverse project drive but will generate hundreds of gigabytes of cached files on your local drive and consume additional GPU memory space at runtime.
Assets in a simulation must also be good citizens of the entire project and use available resources efficiently.
Introducing the Omniverse Texture Cache#
As a practical example of how SimReady assets are allocated memory, when Omniverse first loads a texture, it creates a series of separate images in its cache folder, in specific sizes to use with the GPU. These are in the C:\Users\%USERNAME%\AppData\Local\ov\cache\texturecache
folder on your computer and may have entries like this:
Name |
Size |
---|---|
T_Light_B1_Glass_Albedo.ovtex.0 |
134,217,728 |
T_Light_B1_Glass_Albedo.ovtex.1 |
33,554,432 |
T_Light_B1_Glass_Albedo.ovtex.2 |
8,388,608 |
T_Light_B1_Glass_Albedo.ovtex.3 |
2,097,152 |
T_Light_B1_Glass_Albedo.ovtex.4 |
524,288 |
T_Light_B1_Glass_Albedo.ovtex.5 |
131,072 |
T_Light_B1_Glass_Albedo.ovtex.desc |
49,396 |
T_Light_B1_Glass_Norma.ovtex.0 |
67,108,864 |
T_Light_B1_Glass_Norma.ovtex.1 |
16,777,216 |
T_Light_B1_Glass_Norma.ovtex.2 |
4,194,304 |
T_Light_B1_Glass_Norma.ovtex.3 |
1,048,576 |
T_Light_B1_Glass_Norma.ovtex.4 |
262,144 |
T_Light_B1_Glass_Norma.ovtex.desc |
98,548 |
This Light’s Albedo and Normal texture is an example of a simple surface (a round “jar” shaped tinted glass globe) with a 13Mb Albedo map and a 1Mb Normal map that generated 256Gb of texture data behind the scenes.
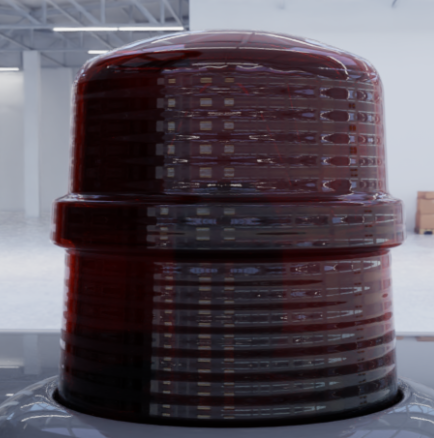
Glass Lamp Lens with Normal and Albedo Bitmaps#
When a bitmap is loaded the first time, Omniverse creates all these “ovtex.x” files, which are transferred to the GPU as required. For this object, the Normal texture is critical for the waves in the glass. However, the Albedo texture could be an RGB value or another bitmap from the project with a Color Tint value. Texture reuse or an RGB color potentially saves hundreds of megabytes of storage and improves performance and memory consumption at startup and runtime.
Simulation PBR Materials#
Robotics and vehicle sensors include LiDAR (Light Detection And Ranging), RADAR (Radio Detection And Ranging), RGB-D, contact, ultrasonic, and IMU. Each of these transducers send and receive signals in a specific electromagnetic (EM) or audible frequency range. Replicating the reflection of these signals from a surface back to the sensor in a physically-based way is critical in vehicle and robotics simulation. This is handled in part with the aid of the next-generation SimPBR materials, specific material naming conventions, and Material Segmenting in the geometry and materials.
The Asset Import process of the Studio Props and Studio Vehicles applications automatically converts materials from OmniPBR into SimPBR and applies settings based on the naming of the material. Properly configuring and naming materials will help ensure the simulation app converts your materials correctly.
Enabling Performance and Memory Statistics#
You can see real-time memory consumption and FPS by enabling them from the viewport “eye” menu:
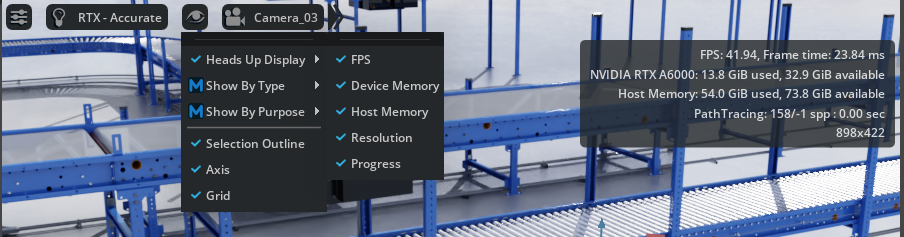
Enabling the Viewport HUD#
Areas of your stage may have different FPS, which can help to identify potential issues with geometry or material complexity.
Profiler#
The Profiler is an Omniverse extension to identify bottlenecks and resource use in your application. It is accessed by pressing F8, or from Windows->Utilities->Profiler.
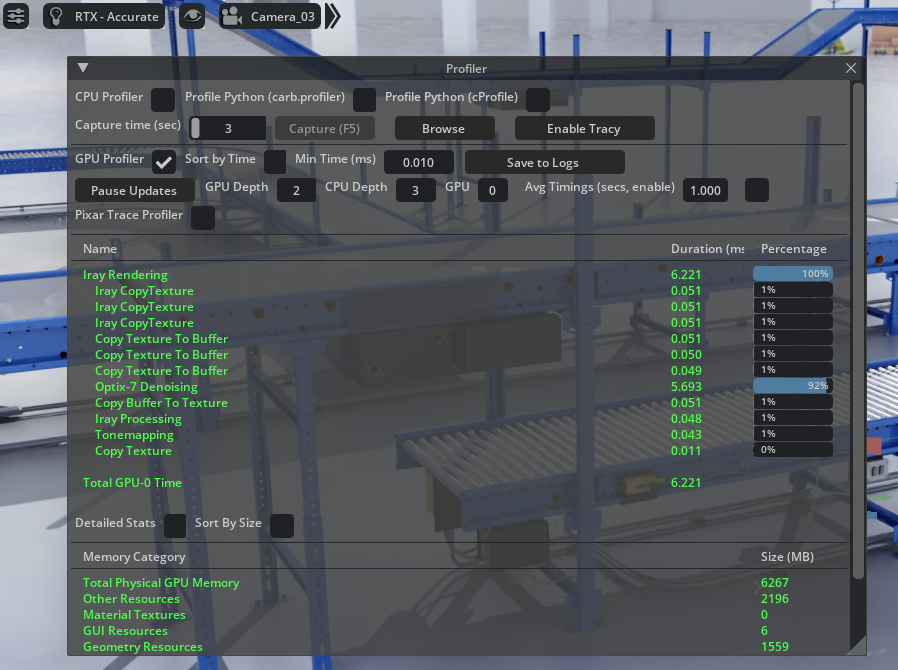
Profiler window showing Iray statistics#
The profiler won’t help identify individual shader issues but can help identify where the renderer spends its time and resources.